I have a friend who owns a successful cement company, drives a Tesla and has solar on his roof.
When I first met him, I assumed that owning a green car and sporting solar on his roof would mean he’d be open to learning about green cement, given that traditional Portland cement is responsible for 7% to 8% of human-caused carbon dioxide (CO2) emissions worldwide.
Cement, by the way, is the glue that holds concrete together.
After chatting over tea one afternoon, I leaned against his Tesla and asked him if he’d consider more environmentally friendly cement.
Trust me, he wasn’t the first to field such questions. I’ve been known for introducing myself to new neighbors with advice about solar and storage incentives. And I’m frequently spotted lecturing random electric vehicle owners about the virtues of time-of-use rates.
So the scene in front of my friend’s Tesla wasn’t unusual.
An attempt to convince a cement company owner to go green
What was unusual, however, was his abrupt rejection of my suggestion and my inability to pique his interest with juicy details about how green cement can be competitive with traditional cement and lower carbon emissions significantly.
Truth is, I didn’t have any of those details–until I was introduced to Ryan Gilliam, a Ph.D chemical engineer who is CEO and cofounder of Fortera, which uses its “ReCarb” process to create cement that can emit 60% to 70% less CO2–even if fossil fuels are used to power the manufacturing process.
Gilliam has launched a few other companies, among them Verdagy, which provides home backup generators and Chemetry (I like the names he chooses for his endeavors!), which is a green hydrogen company.
Heating up limestone yields CO2
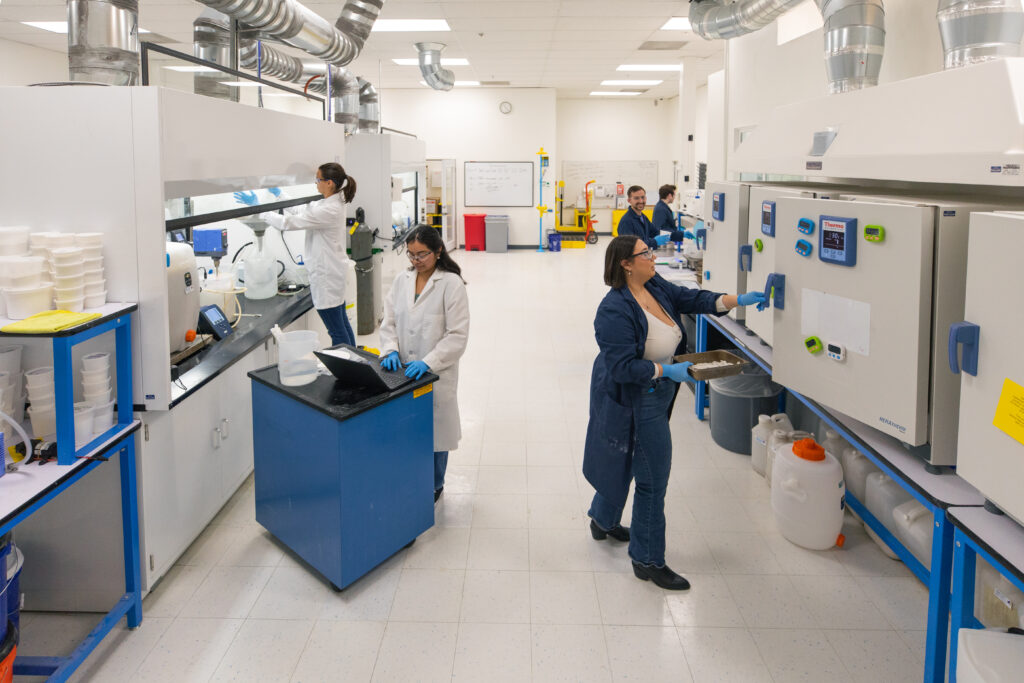
In an interview, Gilliam explained that when cement is made, the CO2 emissions come from production–and the process of heating up limestone is a big culprit.
About 60% of traditional cement’s emissions originate with limestone emissions, and about 40% come from the hydrocarbon fuels used to heat up kilns that heat limestone, he said.
Lowering CO2 emissions 60%–even when using fossil fuels
Fortera’s ReCarb process can create cement with 60% fewer CO2 emissions with its chemistry, even when using fossil fuels to heat up the kiln.
Cement companies can use just some of Fortera’s product in their mix and achieve up to 60% emission reductions, or use higher volumes, and the CO2 emissions can drop by 70%, he said.
Journeying toward zero-emission cement
“What we are focused on is giving cement companies the opportunity to take a journey,” Gilliam said. “We allow them to reduce CO2 now and have a pathway to zero-emission cement in the future.”
Just as important, the company–which is nearing completion of a plant in Redding, California–can achieve these benefits at prices competitive to traditional Portland cement, he said.
How Fortera Cuts Co2 Emissions
The company achieves lower CO2 emissions by capturing the CO2 that comes from heating up limestone, mixing in lime, and then dissolving this mixture into a solvent, or a form of limestone that can be used as a partial cement replacement.
“We take what came out of the kiln and recombine it with CO2 to make a reactive form of limestone,” he said. “In our case, we emit CO2 to make lime, but recapture the CO2. With our ReCarb process, we reduce emissions by 60%.” The company also makes more efficient use of the energy needed to heat kilns.
The plan is for cement companies to add small amounts of the product into their cement when first trying it out, and then possibly add more.
“We are starting off with smaller blends; they fit under the regulations,” said Gilliam. Some of these regulations are designed to ensure that once the product is added to cement, the finished product can hold up as well as traditional cement.
“We want to get to a 70% CO2 reduction. We’re also looking at how to integrate green energy. That’s a parallel effort that unlocks our ability to get to net zero,” he said.
Green cement and concrete companies form an alliance
Fortera isn’t the only green cement or concrete company, and recently joined forces with other green companies to decarbonize the industry with an effort called DC2.
The collective aims to rethink how concrete and cement are processed, create novel materials and utilize or sequester CO2 directly in concrete. Other goals include creating new jobs and reinforcing local economies and supply chains, scaling up the low-carbon cement and concrete industrial base and promoting environmental justice while changing how the products are manufactured.
With details, I hope I can inspire my friend to take action
With the near-completion of Fortera’s plant in Redding and the recent formation of DC2, I think it’s time for tea again with my friend, the successful cement company owner.
I now have many of the details that I need to do a better job of expounding on green cement–and hopefully prodding my friend into taking action.